July 16, 2025
BETA CAE Systems announces the release of
the 2025.1 version of its software suite
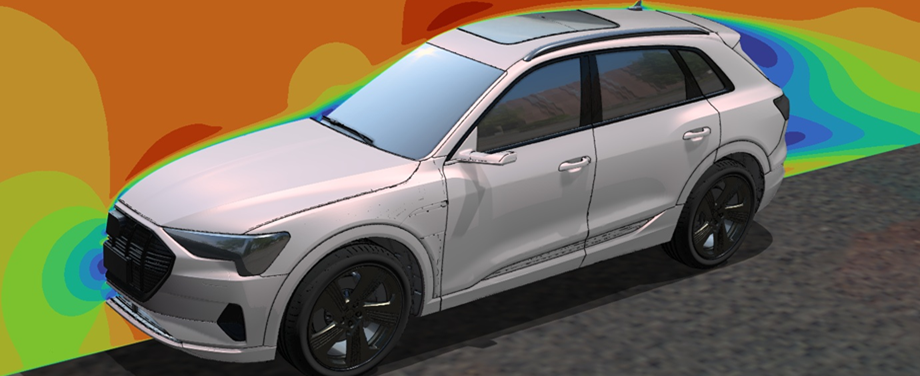
About this release
BETA CAE Systems is thrilled to announce the release of the major version 2025.1 of its product line for ANSA, EPILYSIS, META, KOMVOS, SPDRM, FATIQ, ANSERS and RETOMO.
Marking a new era with a revamped numbering scheme, reflecting the year and the semester per release, this brand-new version offers an increased number of new tools and features, high-level interaction with 3rd-party software, along with elevated performance, enhanced user experience and noteworthy key-features that add value to your daily tasks and processes.
Do not miss:
- The expanded perspective of Modular Environment, now also standing as an end-to-end NVH simulation platform
- The significant enhancements for watertight model preparation for CFD simulations
- The promising functionality of the new Seamweld designer, offering design and customization of the welding representation as per the individual modeling guidelines
- The significant performance improvements for SOL 200 Topology Optimization in EPILYSIS
- The impressive photorealistic experience in render mode, thanks to the introduction of pathtraycing mode in META
- The all-new CAD to CAE workspace, building and maintaining simulation structures with ease in KOMVOS
- The new integrated analysis types in FATIQ, with regards to multiaxial loading and thermo-mechanical fatigue damage calculation
- The advanced flexibility in data querying & sharing in ANSERS
Videos - Latest developments in BETA’s product line
New version Highlights
Elevated user experience in ANSA & META
The redesign of ANSA & META, introduced in prior versions, is further enriched with new features that constantly facilitate daily tasks.
The introduction of Dark Theme, apart from the sleek, modern aesthetic, offers an enhanced user experience, especially in low-light conditions.
Thanks to the new settings’ management, all settings files are now grouped into profiles, enabling cleaner structure, easier sharing, and consistent behavior across environments.
Furthermore, interactive customization of Ribbons allows for tailor-made UI, based on the individual modeling applications and needs.
These enhancements add value to the already introduced innovative UI approach, flattening the learning curve and providing direct access and handy interaction to even non-expert users.
Leveraging pre-processing tasks in ANSA
Along with the elevated user experience from pre- to post-processing, both ANSA & META come with enriched functionality and upgraded performance.
Starting with ANSA, Modular Environment now stands as an end-to-end NVH simulation platform, offering complete management of full vehicle NVH workflows, including automated reduced model generation, efficient “what-if” scenarios creation and run (based either on Full FE or on reduced models), along with robust version control and traceability mechanisms. On top of that, mass creation of reduced models is now possible through an automated process. Thanks to the Solver Submission feature, you can now submit Simulation Runs locally or on remote HPC servers, with real-time monitoring of solver logs and results.
Focusing on the Assembly and Model Buildup process, the introduction of the new Seamweld designer facilitates the user to design and customize the welding representation as per the individual modeling guidelines.
The Sketch 2D ribbon, introduced in prior versions and standing as one of the breakthroughs in ANSA so far, has been enriched with even more features, such as the creation of sketches by projecting or cutting 3D geometry, along with the support of transformations.
Significant enhancements have also taken place in meshing, both for structural and CFD analysis.
Starting from structural, the new Mesh Settings UI guides the user to easily generate the desired mesh based on model type. Meshing of tubes on casting parts has been greatly enhanced, along with the middle curve creation of complex profiles. In addition, a new tool that identifies and connects faces based on proximity has been introduced, enabling efficient generation of volume meshes through node-to-node connectivity.
Focusing on CFD, significant improvements have taken place in quality and gap resolution for Hextreme volume meshing, along with more controls for layers’ specifications and assigned quality criteria. Furthermore, the support of Fidelity CFD solver has been greatly enhanced with an improved Case Setup window, complete material support and native ADIOS2 file output. Watertight model preparation with Fidelity AutoSeal has also undergone significant updates, offering an automatic PID assignment of created patches, reduced number of created elements, along with improved quality, speed and memory performance.
In the Crash & Safety domain, the Dummy Landmark Positioning tool automates and optimizes ATD positioning, by aligning landmarks using physical test data. The new Luggage Impact tool facilitates the positioning of luggage behind seats, supporting ECE R17 and custom cases. Not to be missed, a new approach in airbag folding setup supports model build for Pam-Crash and LS-DYNA solvers. Moreover, BETA software suite keeps integrating all latest protocols in the market; for Pedestrian Safety, GTR-9/UN-R 127-02-03, GB/T China 2024 and JNCAP 2024 protocols and for Low-Speed crash test, GB 17354 protocol.
Design & Morphing implementations come with enriched functionality, such as direct 2D Rib generation with automatic connection to underlying geometry, along with verification of Rib angles, concave areas, thickness, draft angle and more.
Closing with SPH solver implementations, thanks to the integration of Thermal analysis, temperature-based viscosity is now available in dynamic transmissions. In addition, the accurate modeling of high viscous fluids is now a fact in the new version.
Significant enhancements and performance improvements in EPILYSIS
Several noteworthy upgrades come with the release of 2025.1, especially with regards to SOL 200.
In specific, Panel ERP results are supported as design variables and objectives in modal frequency optimization (SOL 200) in combination with AMLS. Focusing on SOL 200 Topology Optimization, the Minimum Gap manufacturing constraint now imposes a minimum separation distance between solid members, while the Casting and Extrude manufacturing constraints have been further enhanced. These come along with a significant performance improvement in Topology Optimization for large scale models that include Casting or Extrusion manufacturing constraints and multiple static loadcases.
Cross-disciplinary efficiency in META
The new version comes with a vast range of new features for post-processing across disciplines.
First, report data from several of the standard Crash & Safety and NVH toolbars can be stored automatically and can be visualized in ANSERS in provided dashlets.
Regarding NVH analysis, unique diagnostic capabilities have been developed by BETA CAE Systems as the outcome of a long research. First, the expanding TPA option in FRF Assembly tool provides the identification of the top N worst paths for a specific frequency for an assembly consisting of multiple components and connectors. Added to this, the influence of modes of any components of the assembly to a response can be assessed offering an insight of how a component can influence a response belonging to another component. Continuing with reduced modeling, external superelements can be used in Modal Response and FRF, including modal participation factors and modal displacement calculation. Focusing on exterior acoustics in Modal Response tool, pressure can be calculated on Field Points using Rayleigh integral method.
Focusing on CFD analysis, a new interactive functionality allows to edit the position of Cut Planes and Flow Paths. Moreover, not only ADIOS2 geometry and result files for FidelityCFDscan are supported, but also case directories for monitor files can be scanned and 2D plots can be directly generated.
META 2025.1 brings user productivity in the spotlight, too.
The introduction of pathtracing allows for a photorealistic experience in render mode, whereas several additional visualization features add value to the existing processes. For instance, thanks to the smart positioning of annotations in 2D plots, we can now avoid overlap with existing plot entities. Visual quality has been improved for 2D plots, along with the undo/redo functionality for these. A simplified user interface of the User Field Function tool provides easier expression definition and, thanks to the multiple scalar fringebars, the simultaneous display for different Scalar or Vector result is now possible in the new version.
Closing with eXtended Reality, with the full support of Varjo XR-4 headset in 2025.1 all VR functionality is supported in Mixed Reality with the press of a button.
Expanded Process Management in KOMVOS
Among the numerous implementations in 2025.1, the initial step from CAD to the interactive CAE structure creation is now performed through a new, dedicated workspace for the CAE structure preview and management.
Process management is now way more efficient, as we can directly create, manage and monitor scheduled tasks. Meanwhile, the redesign of Process Diagram adds value to the new version, with an updated process panel, featuring a new color palette for node states and slots.
In the model buildup area, the brand-new Part Build Orchestrator facilitates the automation for CAD files translation, part type detection and centralized meshing. Moreover, thanks to the HPC Submission, users can submit simulation runs locally or on remote HPC servers, with real-time monitoring of solver logs and results. Also, SPDRM administrative tasks can be carried out directly within KOMVOS, thus further accelerating SPDM processes and workflows.
Lastly, focusing on Machine Learning, there is a new API for simulation results and mode classification prediction tasks and features can be extracted remotely, through SPDRM, for non-parametric/ cross model/ Machine Learning models.
Scale simulations with confidence, agility and control with SPDRM
The latest release of SPDRM marks a major step forward in simulation process and data management, combining modern infrastructure, smarter workflows, and stronger data control to help engineering teams work faster, more securely, and at scale.
This version introduces major infrastructure updates, including a move to Java 21 and WildFly 32, boosting performance, security, and compatibility with modern standards. Authentication is now more flexible with support for OpenID Connect and Keycloak integration, while both on-premise and cloud deployments benefit from enhanced failover mechanisms using Nginx and AWS Auto Scaling Groups.
Process design is more versatile than ever, with support for new variable types binary data and structured lists, and the addition of an Event Listening node that enables dynamic, signal-driven workflows. Real-time solver log broadcasting adds further transparency to simulation execution.
New built-in workflows include the Part Build plug-in for part-level preprocessing, the HPC Submission plug-in for streamlined run submission, and ready-to-use optimization templates to accelerate custom workflow creation.
On the data management front, SPDRM now integrates with Amazon S3 Glacier for cost-effective archiving, improves cross-environment data migration, and enhances schema editing in KOMVOS with more robust attribute and alias operations.
New calculation methods and boosted performance with FATIQ
The new release comes with upgraded FATIQ features and implementations with regards to calculation methods, run management and user productivity.
In specific, thermal fatigue analysis has been integrated in FATIQ, supporting temperature dependent materials and thermal loads. In addition, a new, complete analysis for multiaxial models Fatemi-Socie and Smith-Watson-Topper in ε-N analysis, as well as the Findley model in S-N mark their presence in the new version.
Furthermore, results’ files are now organized with more convenient structure and file names and annotations can be created and managed effortlessly on points of interest.
Enhanced flexibility in data querying & sharing with ANSERS
Sharing of dashlets’ visualizations has greatly advanced with the introduction of team templates, shared and used by a whole team and with ways to share reports to specific users, or other teams. Users can now be also grouped in teams, to facilitate the above scenarios.
Moreover, setting up new dashlets or extending existing ones is now much easier with the introduction of library items - standard blocks of commonly used data transformations and visualizations.
Together with enhancements in META tools, the new version offers an easy-to-use solution for having results of standard loadcases stored in a DM system and viewing them in ANSERS. META tools handle the data storage implicitly, whereas dashlets suitable for each analysis are offered by us. Such cases include Occupant Injury, Pedestrian, IIHS, Eigenmodes and CFD analyses.
Lastly, following up the implementations of the previous versions, ANSERS 2025.1 is enriched with a set of new types of charts, along with new panel types.
Documentation Transition to HTML format in BETA Product line
In our ongoing efforts to enhance user experience and accessibility, we have transitioned from traditional monolithic PDF documentation to HTML format.
This modern approach offers several key benefits:
- Improved Accessibility: Users can now easily navigate and search through the documentation online, ensuring quick access to the information they need.
- Enhanced User Experience: The documentation is organized in a more intuitive structure, with hyperlinks and cross-references facilitating seamless navigation between related topics.
- Interactive Features: Incorporation of interactive content, such as code examples and videos, providing a more engaging learning experience.
- Easy-to-Translate: This new format will allow for swift and seamless documentation translated in other languages upon demand.
Compatibility and Supported Platforms
ANSA files saved by all the first and second point releases of a major version are compatible to each other. New major versions can read files saved by previous ones but not vice versa.
META Project files saved from version 24.1.2 are compatible and can be opened by META version 16.0.0 or later.
Support for Mac OS has been discontinued.
Support for 32-bit platforms has been discontinued for all operating systems.
Download
Where to download from
Customers who are served directly by BETA CAE Systems, or its subsidiaries, may download the new software,
examples and documentation from their account on our server. They can
access their account through the "download" link on our website.
Contact us if you miss your account details. The Downloads menu items
give you access to the public downloads.
Customers who are served by a local business agent should contact the local support channel for software
distribution details.
What to download
All files required for the installation of this version reside in the folders named "BETA_CAE_Systems_2025.1.0", "KOMVOS_2025.1.0", "RETOMO_2025.1.0", "FATIQ_2025.1.0", and "ANSERS_2025.1.0", and are
dated as of July 16, 2025. These files should replace any pre-releases or other files downloaded prior to that date.
The distribution of this version of our pre- and post-processing suite is packaged in one, single, unified installation file, that invokes the respective installer and guides the procedure for the installation of the required components.
For the installation of the software on each platform type, download from the respective folders, the .sh file for Linux or the .msi file for Windows.
In addition to the above, optionally, the META Viewer is available to be downloaded for each supported platform.
The tutorials and the example files reside in the folder named "TUTORIALS". This folder includes a complete package, and one with only the updated files.
The Abaqus libraries required for the post-processing of Abaqus .odb files are included in the installation package and can be optionally unpacked.
Earlier software releases are also available in the sub-directory called "Previous_Versions" or in a folder named after the product and version number.